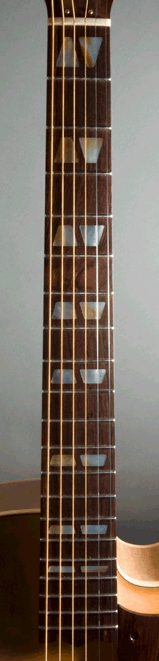
17” guitars have a scale length of 25 and 3/8”, the same as a modern L-5.
16” guitars have a 25” scale, a bit longer than an ES-175, for better string tension and a bit more room in the upper register.
In the past, I have made 18” guitars with a scale length of 25 and 3/8”, but I have upgraded my 18” model to now have a scale length of 25 and 1/2”. I think the slight increase in string tension is a good thing on a big guitar.
I have made guitars with 1 and 3/4” nuts, but I have changed my standard models to now be 1 and 11/16”. That seems to be what is most comfortable for the majority of players, myself included. The width at the 12th fret is 2 and 3/32”, a bit more than a 1 and 11/16” nut Gibson, but a bit less than a Martin D-28.
Fret slots are CNC machined to an accuracy of 1/10000 of an inch.
The finger board has a compound radius: I am now using 9” at the nut and 15” at the 20th fret. This is not just to facilitate string bending. The compound radius makes the action height much more consistent across all the strings, up and down the finger board. Since the finger board increases in width, it should not simply be a section of a cylinder. Visualize the finger board as a section of a cone, and you may understand the need for a compound radius.
16” guitars have a 25” scale, a bit longer than an ES-175, for better string tension and a bit more room in the upper register.
In the past, I have made 18” guitars with a scale length of 25 and 3/8”, but I have upgraded my 18” model to now have a scale length of 25 and 1/2”. I think the slight increase in string tension is a good thing on a big guitar.
I have made guitars with 1 and 3/4” nuts, but I have changed my standard models to now be 1 and 11/16”. That seems to be what is most comfortable for the majority of players, myself included. The width at the 12th fret is 2 and 3/32”, a bit more than a 1 and 11/16” nut Gibson, but a bit less than a Martin D-28.
Fret slots are CNC machined to an accuracy of 1/10000 of an inch.
The finger board has a compound radius: I am now using 9” at the nut and 15” at the 20th fret. This is not just to facilitate string bending. The compound radius makes the action height much more consistent across all the strings, up and down the finger board. Since the finger board increases in width, it should not simply be a section of a cylinder. Visualize the finger board as a section of a cone, and you may understand the need for a compound radius.
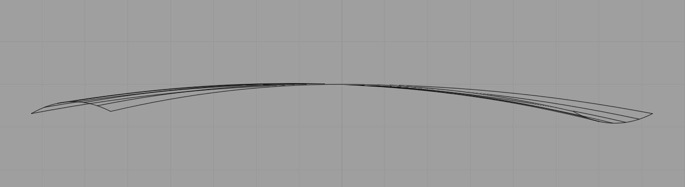
The fingerboard surface is milled into a graduated relief which is 1/64" negative on the treble side, dead level down the middle, and 1/64" positive on the bass side. Under string tension, it pulls up more on the treble side, resulting in approximately a 1/64" relief differential. A double action truss rod allows me to adjust the surface in order to prepare for fret installation or adjust the proper relief under string tension. This produces great playability with a minimum of thickness variation in the fingerboard overall. I can make the inlay pockets follow this complex surface. The inlays and fingerboard surface need only a minimum of sanding to clean up the machining marks, and I will not be sanding inlays thinner in some places than anywhere else. In the above illustration you are looking down the fingerboard from the nut, towards the bridge; you can see the negative relief on the treble side at your left, and the positive relief on the bass side at your right.
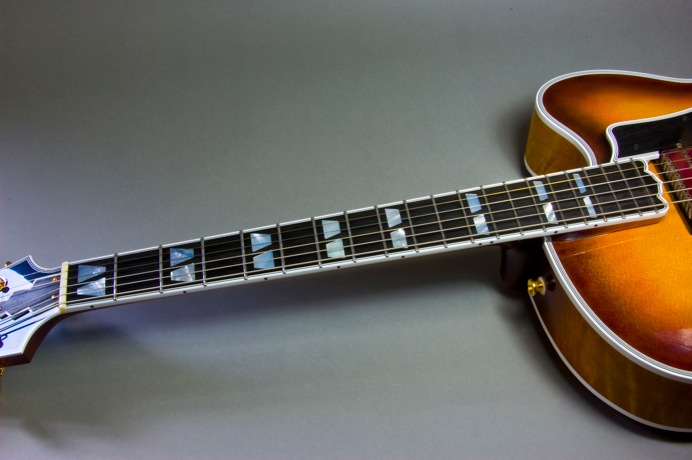
The frets are Jescar stainless steel, part number FW55090-S; width is .090” and height is .055”. Jescar fret wire is manufactured to very close tolerances, so that little milling is required if the finger board has been well prepared and the frets have been installed properly. This is a tall medium fret wire that provides superior durability and playability. Intonation is excellent, and the medium width makes moving up the neck, and grabbing chords in the upper register much easier than with jumbo fret wire.
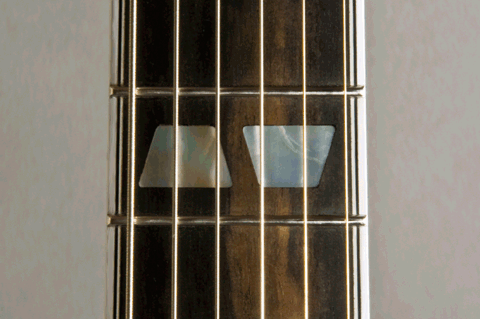
Skylark and Pannonica guitars have bound finger boards.
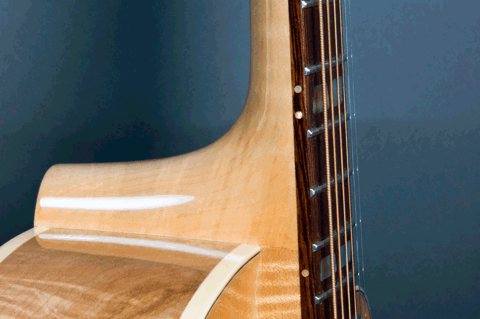
Skylark Spirit and Pannonica Spirit finger boards have no binding, but the fret slots are margin delimited. That is, the fret slots are machined slightly shorter than the width of the finger board, so that the fret slot and fret tang are not apparent at the edge of the finger board. This makes the edge of the unbound finger board feel as smooth as a bound finger board.